Sublime
An inspiration engine for ideas
Picture it. One Ford employee making ten cars a year for thirty-five years while his Toyota counterpart goes from four to sixty. Toyota’s supplier network? A typical GM car factory used eight hundred suppliers. Toyota? Just 125 … with half the in-house work. This dispels the Western myth of needing more to do more: Toyota was doing more with less.
... See moreJohn Willis • Deming's Journey to Profound Knowledge: How Deming Helped Win a War, Altered the Face of Industry, and Holds the Key to Our Future

That was the genesis of what has been called MBWA. I learned that quality requires minute attention to every detail, that everyone in an organization wants to do a good job, that written instructions are seldom adequate, and that personal involvement is essential.
David Packard • The HP Way: How Bill Hewlett and I Built Our Company (Collins Business Essentials)
Deming’s System of Profound Knowledge encompasses four elements and includes fourteen points of management and seven deadly diseases of management. These four elements of Profound Knowledge are: 1. A Theory of Knowledge: How do we know what we believe we know? 2. A Theory of Variation: How do we analyze and understand what we know? 3. A Theory of P
... See moreJohn Willis • Deming's Journey to Profound Knowledge: How Deming Helped Win a War, Altered the Face of Industry, and Holds the Key to Our Future
guide change management activities
Jeffrey Hiatt • ADKAR: A Model for Change in Business, Government and our Community
The value chain is another Porter framework that managers refer to all the time. Most, I believe, know what a value chain is—the metaphor of a series of linked activities is intuitive. But many miss the “so what.” Why does it matter? The answer: The value chain is a powerful tool for disaggregating a company into its strategically relevant activiti
... See moreJoan Magretta • Understanding Michael Porter: The Essential Guide to Competition and Strategy
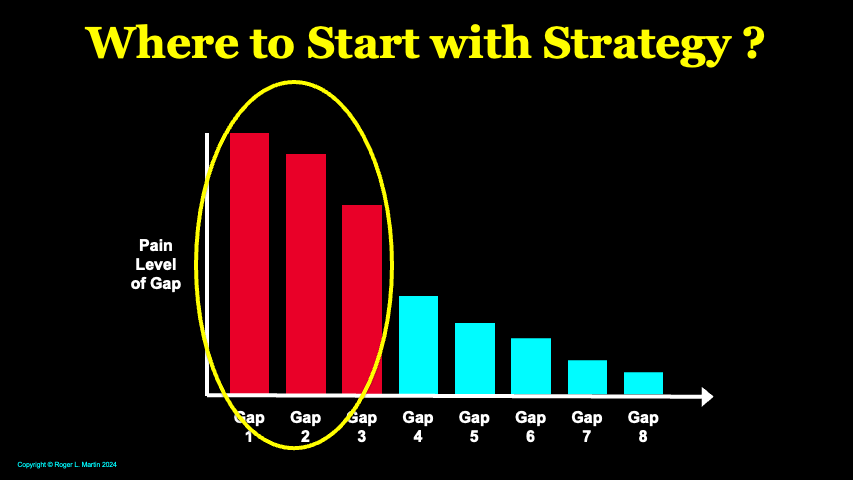
The paradox is that when managers focus on productivity, long-term improvements are rarely made. On the other hand, when managers focus on quality, productivity improves continuously. John Seddon
Jez Humble, Joanne Molesky, • Lean Enterprise: How High Performance Organizations Innovate at Scale
Whatever it is called, the underlying principle is that improvements come from reexamining the details of how work is done, not just from cost controls or incentives.